Gilles Van Mol, OilSense, Dec. 1, 2023 | Like top athletes who engage in their passion with perseverance, I also find my life’s fulfilment in embracing my own passion. Just as they refine their skills and push boundaries, I leverage my expertise to explore new avenues within the field of industrial oil management, where acts of engineering present distinct opportunities for me to unleash my creativity. This journey extends beyond mere problem-solving; it’s an expression of my deep-rooted passion that propels me consistently to innovate and contribute to the evolution of industrial oil management.
It truly is an interesting field of exploration, worth a lifetime’s dedication. Here’s my journey….
I worked day and night to refine my prototype device until it was ready for presentation to the jury. But designing a particle counter was, in fact, just the beginning.
The start
My story started about twenty years ago, when I embarked on a journey to obtain a master’s degree in electromechanical engineering, and I had to pick a challenging thesis topic. Despite my interest in thermodynamics, a unique opportunity presented itself when I came across a project on particle detection in lubricating oils.
One of the functions of an industrial oil is to provide lubrication and, by doing that, to prevent metal-to-metal contact. I learned that particles present in the oil disrupt the oil film and cause damage to machinery parts like bearings, gears, valves, etc. This damaging process generates even more wear particles, ultimately resulting in irreversible damage and premature machine failure. I was intrigued by the prospect of designing an online oil particle counter that could continuously measure and display the particle concentration in the analysed oil.
This project was no easy feat, considering the microscopic size of the particles and the sheer volume of wear particles present in used oils. In just 1ml of analysed oil, there could be as many as 30,000 particles! To obtain representative results, I had to measure enough oil every minute, all while complying with the industrial ISO 4406 standard, which required classifying particles larger than 4 microns, 6 microns, and 14 microns.
Over the course of six months, I tirelessly programmed microcontrollers that were fast enough to detect and quantify these particles so small that they are even invisible to the naked eye. I worked day and night to refine my prototype device until it was ready for presentation to the jury. My hard work and dedication paid off when I proudly demonstrated a working device that could continuously monitor oil particles with great precision. (And, yes, I was awarded my master’s degree.)
From layman to specialist
Designing a particle counter was, in fact, just the beginning. Although important, it’s a small part in a bigger concept called industrial oil management, which covers all activities that must be performed to keep lubricating oil in optimal condition throughout a machine’s lifecycle. With such activities, we aim to reduce machine shutdowns and maintenance costs, ensuring maximum machine availability and resulting in a significant return on investment.
I was fascinated by the concept of industrial oil management, but at that time I was a novice in the field. I quickly learned that certain criteria are crucial to maintain oil in optimal condition. For example, oil sampling, oil analysis, or oil filtration are essential, along with the understanding that there are different types of industrial oils, such as hydraulic oils, transformer oils, and turbine oils.
Fortunately, my pursuit of International Council for Machinery Lubrication (ICML) certifications required me to attend top-notch training courses covering all of these aspects and providing specialized knowledge. Over the years, I have acquired most ICML certifications, including MLA III, MLT II, LLA II, VPR, and VIM. Though this is a continuous learning process, these training courses are a must for anyone involved in the field of industrial oil management. Through these certifications, I have improved my skills and expertise, allowing me to tackle complex challenges and drive innovation in this field.
Investment in oil management pays off for both small and large companies, leading to significant cost savings and increased machine availability.
Charting my own path with OilSense
In 2014, I decided to put my knowledge and experience to good use by launching my own company, OilSense. The goal was to provide consulting services, training courses, and audits. By conducting on-site audits, I’m able to identify areas where oil management practices can be improved. I take a snapshot of the current practices and search for weak points that can be addressed. This involves investigating and evaluating around ten different oil management categories, each with a multitude of subcategories. By examining whether the client takes representative oil samples, analyses the right oil parameters, and prevents oil contamination, among other activities, I can provide valuable insights and recommendations for improvement. This investment in oil management pays off for both small and large companies, leading to significant cost savings and increased machine availability.
In 2022 I had the opportunity to perform an audit of the Large Hadron Collider particle accelerator at a division of CERN. This was an exciting and challenging project, and it felt very rewarding to apply my expertise in a cutting-edge, high-tech environment.
One of my favourite aspects of this work is sharing my knowledge by providing three-day courses myself, based on ICML’s Body of Knowledge. While oil management practices were implemented only sporadically in the early 2000s, interest in this area has significantly increased the past few years. This is evident in the growing number of individuals pursuing education and certification in machinery lubrication. While instructing these courses, I ensure that all questions are answered, and I value the feedback and experiences shared by the participants. As an expert in the field, it’s gratifying to see others develop their skills and knowledge and, for their part, contribute to the ongoing advancement of machinery lubrication.
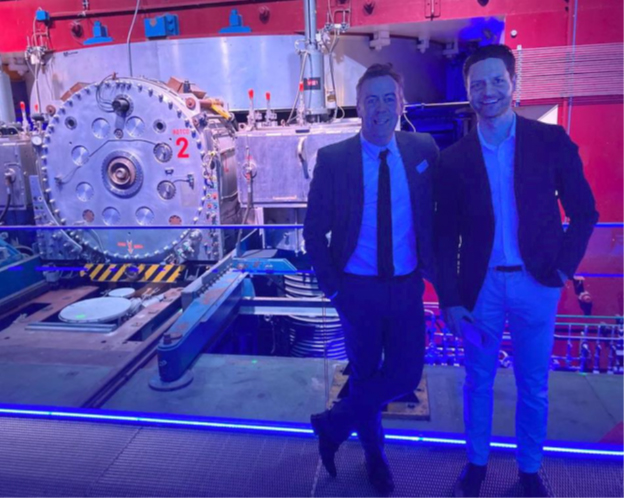
Picture 1: Gilles (right) at CERN’s first accelerator, the Synchrocyclotron. With Steve Mattens of Flanders Investment and Trade (wearing necktie).
Passion projects with OilSense engineering
In 2018, I was intrigued by the idea of combining my engineering expertise and my knowledge of oil management to design complete oil filtration machines. Along with a college friend, we aimed to improve the existing offline oil filtration practices.
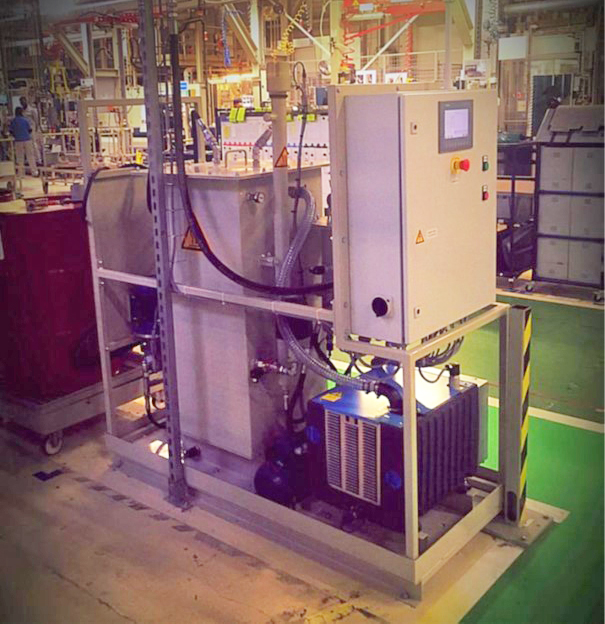
Picture 2: OilSense customized vacuum dehydrator
While vacuum dehydrators are available in the market to remove dissolved water in industrial oils, their efficiency decreases with high viscosity oils or when there is a large amount of free water present in the oil, for instance, due to a cooler leakage. However, after investing considerable time, we managed to design a machine that can remove large amounts of free water in a short time and simultaneously remove dissolved water to very low levels, even for high viscosity oils. As we master the complete design, we can produce customized vacuum dehydrators that are able to filter used oils to an ultra-pure state with a particle concentration less than 12 / 9 / 4 according to ISO 4406, and a water concentration less than 10 ppm.
Picture 2 shows an example of this type of machine, which is also capable of directly communicating with the factory’s production line controllers through the integrated PLC.
Designing an offline oil filtration machine that could be safely used in potentially explosive atmospheres (ATEX zones) was another challenge we encountered. In such atmospheres, machinery is located in places where a mixture of gases or dusts combine in ways that could lead to ignition. The last thing one wants to happen in such an atmosphere is an electrical short circuit. However, a dry running pump, for instance, is also a potential ignition source due to the heat generated. And think about the risks posed by the build-up of static electricity… Therefore, we had to use special materials in combination with a lot of monitoring sensors.
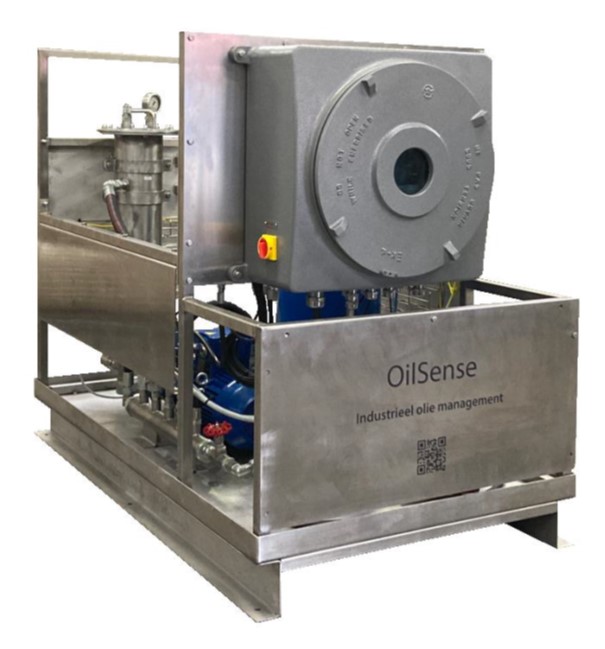
Picture 3: OilSense ATEX unit
Picture 3 is an example of an ATEX-certified offline filtration machine that we designed. Particle filtration, oil dewatering, and varnish filtration are integrated, along with an ATEX oil heater, ATEX particle counter, and water sensor. The user can connect with an ATEX smartphone to view the display and adjust the filtration speed, for example. Moreover, through a wireless connection, the customer can be alerted when the machine is in fault status, and remote monitoring of the machine status is also available.
I’m convinced that an offline filtration unit is an essential component that should be continuously connected to the main oil machine. In addition to filtering particles and varnishes out of the oil, it should also remove excessive water. Integrated heaters are crucial here in regulating the oil temperature more efficiently and accurately than heaters integrated in the oil reservoir, where there is a high risk of oil burning due to little oil movement.
Furthermore, oil analysis sensors have become more affordable and ideally can be integrated into the offline filtering machine. Therefore, we have designed a unit equipped with sensors to analyse particle concentration according to ISO 4406, as well as water concentration, temperature, density, kinematic viscosity, and chemical composition. If the predefined alert or alarm limit is exceeded, the factory’s control room is alerted and immediate actions can be taken.
The innovative future
All my efforts and sacrifices have been worthwhile, as I have designed machines that are now running at large manufacturing companies such as ArcelorMittal, Daikin, or DuPont. Their positive feedback has been heart-warming. However, my journey does not end here. On the contrary, I am more ambitious than ever. Until now, I have only been able to offer my expertise to customers mainly located in Belgium or the Netherlands, one project at a time. I believe that these tailor-made machines could be useful to many other customers outside my region.
Worldwide, the importance of ESG frameworks significantly increases. I strongly believe that industrial oil management plays a key role in reducing the environmental impact of industrial operations by promoting energy efficiency and reducing waste. By maintaining the quality of lubricating oil and minimizing machine downtime, industrial oil management can help extend the lifetime of machinery and the oil itself, thus leading to lower greenhouse gas emissions, reduced waste, and more sustainable operations, while also increasing return on investments and lowering the impact on nature.
I am always on the lookout for international companies that share my passion for innovation. Through collaboration, I could expand my network and allow my designs to be used worldwide to tap the unlimited potential of industrial oil management.
I hope that my next twenty years will be just as thrilling as the first twenty. I am committed to staying in this field of oil management. Who knows, maybe I’ll write a sequel in 2043. To be continued…
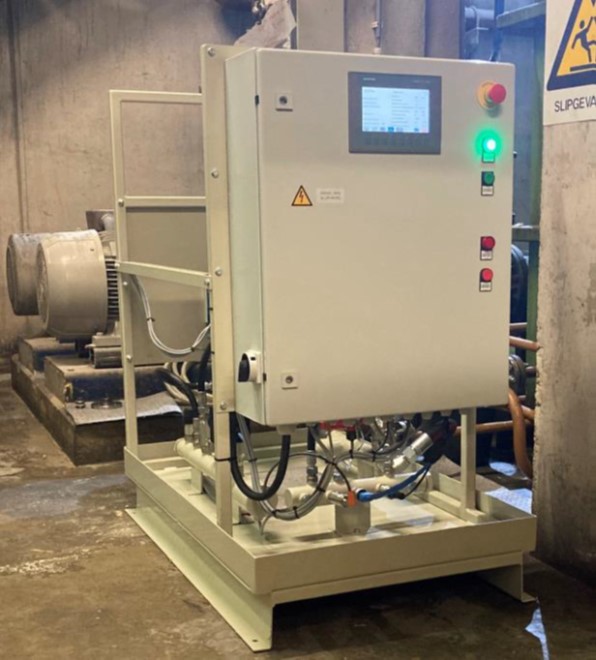
Picture 4: OilSense Oil Condition Monitoring unit