Michael D. Holloway, 5th Order Industry, July 22, 2021 | About 2 million farms are currently in operation in the United States. Corn and soybeans account for over 40% of US crops. In 1900, the average yield in the United States of corn per acre was 25 bushels, in 1965 it was 80 bushels, and by 2000 the average yield of corn was 140 bushels. The increase in productivity was due to the implementation of larger, more reliable equipment, hybrid seeds that were draught- and herbicide-resistant, improved fertilizers and pesticides, and an increase in data for improved planting. In 1900, it took 38 hours to plant, cultivate, and harvest one acre of corn. By 1965, it only took 6 hours, and in 2000 it took less than an hour. The increase in productivity and yield is similar with that of other crops, as well (wheat, soy, other grains). The acre rate per hour varies due to crop, location, equipment, and conditions.
A farm tractor provides most of the work, with the implement choice depending upon the job. The tractor uses a universal hydraulic system with a special oil responsible for the wet-brakes, transmission, steering, all hydraulics, and the PTO that operates the implements. Thermally stressing the fluid will shorten the life of the oil by increasing the oxidation rate which will increase the acid formation in the oil leading to deposit formation. Because of the application, a universal hydraulic fluid is one of the most additive-rich lubricants.
Tractor Economics
A tractor will work a typical field at least 6 times throughout the year. Depending upon what must be done, the speed at which a task is carried out will vary the cost of operation. The following table is a summation of Iowa State University’s 2020 Iowa Farm Custom Rate Survey report. This extensive report is used to understand the cost of production to determine the overall profit margin for a working farm. These figures establish a baseline of expenses, provided there are no additional costs associated to equipment failure. The Acres/Day estimate is calculated for an 8-hour day.
Working the Ground | Acres/Hr. | Rate/Acre | Acres/Day | Cost/Day |
Till / Disc | 10 to 25 | $7 to $22 | 200 | $4,400 |
Fertilizing (cost minus chemical) | 20 to 30 | $6 to $14 | 240 | $3,360 |
Herbicide Spraying (cost minus chemical) | 60 to 80 | $7 to $10 | 640 | $6,400 |
Planting (cost minus seed) | 5 to 50 | $19 to $24 | 1,200 | $28,000 |
Pesticide Spraying (cost minus chemical) | 60 to 80 | $7 to $10 | 640 | $6,400 |
Harvest (grain, soy, corn) | 10 to 20 | $35 to $54 | 160 | $8,640 |
A 2,400-acre corn farm producing 140 bushels per acre at a sell price of $4/bshl, will yield 336,000 bushels for $1,344,000 in total gross sale.
Working 2400 Acres | Total Days | Total Cost |
Till / Disc | 12 | $52,800 |
Fertilizing (cost minus chemical) | 10 | $33,600 |
Herbicide Spraying (cost minus chemical) | 3.75 | $24,000 |
Planting (cost minus seed) | 2 | $56,000 |
Pesticide Spraying (cost minus chemical) | 3.75 | $24,000 |
Harvest (grain, soy, corn) | 15 | $129,600 |
The machine cost to produce 336,000 bushels of corn is $320,000. The cost does not consider herbicides, pesticides, seed, labor, fuel, insurance, land mortgage, taxes, and equipment loans. Crop and location play a large role in profitability. Weather factors such as hail, drought, floods all have an impact on profitability. Changes in the geo-political landscape–such as changing trade policies as well as tariffs–have an influence as well. The USDA reports that the total average household income among all farm households is $72,481, typically relying on off-farm employment.
Equipment reliability is important in agriculture due to the narrow window of opportunity for planting and harvesting crops. When a critical machine such as a tractor, combine, grain wagon, or various implements such as planters and sprayers experience failure, machinery must be rented until repairs are complete. The typical rental costs for a tractor is $40 to $60 per hour. The cost to rent a combine would be $8 to $18 per acre; therefore, renting a combine can cost as much as $3,000 per day. If the combine must be rented for the entire harvest it would cost $45,000. It is not unheard of for a tractor or combine to miss an entire planting or harvest window of opportunity due to extensive engine or transmission repairs. Many failures could be avoided by using oil analysis.
Farmers will often repair their own equipment if the task is manageable and parts and tools are available. However, a catastrophic failure may have to be repaired offsite and can take several days to several weeks, provided the repair shop’s schedule has availability. After all costs have been estimated, the total ownership cost per hour can be added to the operating cost per hour to calculate total cost per hour to own and operate the machine.
-
- Repair, fuel, lubrication, and labor costs are added to calculate total operating cost. For the typical farm tractor, the total operating cost is estimated to be $60 per hour. When a failure occurs for a combine or tractor to be repaired, it will require transport to the repair facility.
- The ownership costs (also called fixed costs) include depreciation, interest (opportunity cost), taxes, insurance, and housing and maintenance facilities. All told, this is approximately $50 per hour of operation.
Thus, the total cost for this asset is $60 + $50 = $110 per hour of operation. The Agricultural Machinery Management Standard published by the American Society of Agricultural Engineers provides a simplified rule of thumb for estimating the annual cost of repairs as 3% of purchase price for machines owned for 5 years or less.
Identifying Oil Issues
Tractors and combines provide most of the work produced on the farm. Oil analysis has been an important tool to help curtail increased operating costs by identifying the emergence of wear, the condition of the oil, and contamination from fuel, coolant, or washdown chemicals. Lubricants have several functions: reduce friction and wear, transfer power, act as a seal, clean and flush surfaces, keep contaminants in suspension, and protect against rust, corrosion, and oxidation. These are all well-known functions. A lesser considered function, yet no less important, is to act as a conduit of information. The lubricant can provide insight into what is occurring within a system without having to disassemble and inspect.
Prior to an oil sample being drawn for analysis, it is prudent to consider the following observations; overheating, high vibration, high system pressure all may indicate it is time to analyze the oil. The first indication of a problem may be an increase in wear metals (Fe, Pb, Sn, Al, Cu) over a period of several past tests. These metals are common in engines, hydraulics, and transmissions. Oil analysis started as a form of equipment management to increase equipment reliability, extending equipment life with the benefits of increased production efficiency. Farmers have also discovered that oil analysis can increase equipment resale value. Oil analysis can help develop proper lubrication management through reduced lubrication cost savings, establish optimal oil drain Intervals (optimal drain intervals does not always relate to extended drain interval), as well as help consolidate oil inventory. Maintenance management has been a focus due to improved record keeping as well as data analysis. This strategy helps reduce maintenance costs by helping avoid catastrophic failure and reduced downtime. Many agricultural equipment manufacturers and oil blenders are offering oil analysis as a means to provide backup for warranty claims.
While tractors find use on the farm throughout the year, combines are used during the harvest phase of farming. For many crops this may only be for two to three weeks out of the year. Prior to harvest, an oil sample can be drawn to provide data on the health of the system. It’s a common practice to start the combine up and run it through a mock-harvest cycle and access any issues prior to a harvest. An oil sample is typically taken during this phase as well as midway through a harvest cycle. The results are often requested to be provided as soon as possible in order to curtail a potential failure (sometimes same-day service is required). Common issues that can be caught prior to a catastrophic event include fuel dilution or coolant in the engine oil, increased wear metals and particulate in the universal hydraulic fluid, and severe oxidation due to extended operation. Tractors can experience many of the same issues as combines with a greater potential for failure due to their extended idle times as well as their use for other tasks that can produce stress on the system.
sOLVING ONE PROBLEM COULD CREATE ANOTHER
Here is a case where a four-wheel drive, 110hp farm tractor sheared the rear differential pin (see image below). A universal hydraulic oil is the lubricant and is changed annually. The tractor is used for many jobs. In this instance, the tractor was used to pull a 1000-gallon sprayer with a 20ft stainless tower. The asset was used in four-wheel drive and operated on flat ground as well as a 45-degree incline to breach hills. The tractor experienced an overload condition with the full weight of the tower resting on the hitch, and the rear differential pin sheared. The initial solution would have been to avoid excessive load of the tank in the first place. Unfortunately, such a preventive solution is not always possible. Often heavy equipment operators (including farmers) will push their equipment to its operational edge in order to get the most productivity. There are other solutions. To relieve the high torque burden on the differential, a higher engine RPM would have to occur, because at low/medium engine RPMs the torque is higher, producing strain on the pin and leading to the pin shear failure.
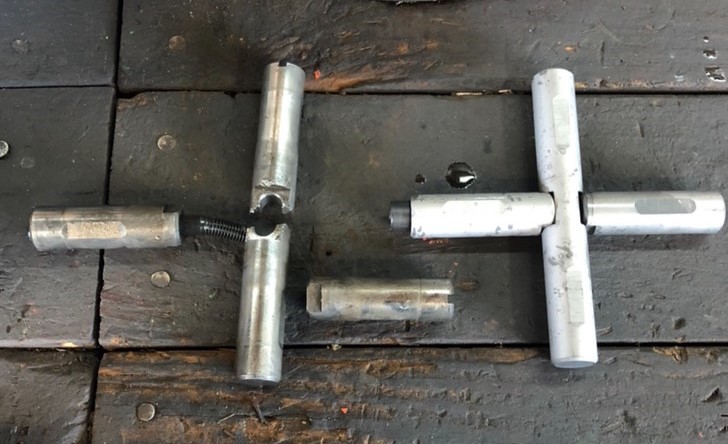
Although increasing engine RPM is a viable solution to avoid future shearing incidents, oil analysis can determine whether the engine’s oil can handle that solution, because increasing the engine’s RPM also increases the operating temperature of the oil. Unmonitored, acid generation and thermal stress combined with the opportunity for water contamination will lead to oil oxidation and the development of sludge and varnish on the components, which would drastically reduce oil performance and change the oil’s viscosity; all this could lead to equipment failure. By using oil analysis, the wear, contamination, performance, and oil condition can be understood with a possible remedy. In this particular case, the remedy might call for a lubricant formula that would hold up better at higher temperatures, perhaps a full synthetic oil that would accommodate thermal stress better than a mineral-based fluid the next time the farmer attempts to pull that tower over a hill.
Oil analysis is often used as a predictive tool to isolate problems within the asset’s components as well as to increase understanding of the overall health of the machine and oil, thus helping farming businesses to maintain economic viability through reduced operational and ownership costs.