Garrett FitzGerald, March 13, 2024 | Condition Based Maintenance (CBM)—and specifically, in this case, the use of oil sample data to deliver CBM—is not a new concept across industry. However, taking a representative sample from an asset and subsequently topping up the oil level can prove to be challenging on assets with high utilization rates or batch-based operation.
Background
Within the IE43 facility at Eli Lilly & Company, Kinsale, Ireland, the maintenance team (which includes ICML-certified MLA II practitioners) is responsible for the management of over 40K assets. This process is administered through the CMMS. PM’s will have a frequency of occurrence and a defined window within which they must be completed. Before works can commence, they must be scheduled and the equipment made safe. Aligning these tasks across multiple assets within the allowed time, historically was a stumbling block. Furthermore, assets as supplied by OEM’s are not designed to facilitate oil analysis or reduced maintenance interventions.
Oil changes are only scheduled when the data indicates this is required. In this way the oil becomes part of the asset and not simply a consumable to be replaced.
When planning to deliver a new Oil monitoring program as part of a wider Condition Based Maintenance strategy for the IE43 facility, finding a technical solution to these challenges would prove to be key to successful implementation.
Asset Criticality
As mentioned above, within IE43 the maintenance team manages 40K assets, so key to how these are managed are criticality rankings. Approximately 900 rotating assets makeup a subset of the overall number, of which 420 are routinely lubricated. Almost twenty percent of these (i.e., 90) are deemed the most critical and targeted for additional monitoring.
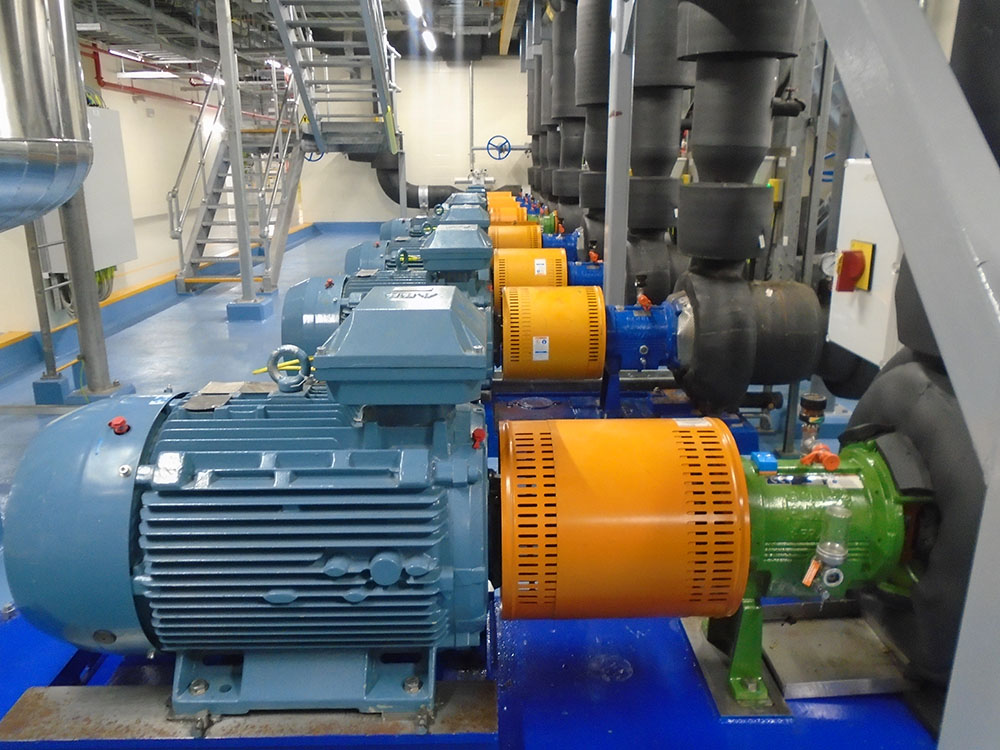
Figure 1: IE43 LGF Utility Glycol Return Pumps
Following identification of the asset list to be sampled, it was necessary to design specific sampling solutions based on asset type and location. Selection of suitable sampling technologies along with custom mechanical fittings was required.
A key step towards mitigation of project risk was to develop an external partnership with access to required expertise and suitable hardware to facilitate implementation.
With technical solutions identified and procured, installation was completed by the onsite craft and utilities teams.
Challenge & Solution
Equipment access can be a key challenge when trying to complete CBM type activities. To be of use, data gathered must be representative, and when it comes to oil samples this means the samples need to be uniform and thus taken from the mixing zone. Continuous online monitoring is a good solution but is not practical in all cases. Deployment of an oil sample route can be a good substitute—but there are three key criteria that must be met for that data to be useable. Data must be:
- Safe to gather.
- Repeatable.
- Representative.
A lubrication management strategy is now embedded in the IE43 facility. The foundation of this is a site SOP built on the ICML 55.1 Standard.
Historically onsite, a sample could only be taken when the asset was at rest and locked out. To successfully complete the task in such a case, several steps would need to be completed:
- Sample requested by the maintenance team.
- Added to the production schedule.
- Locked out by permitter.
- Sample taken by craft.
- Oil top-up.
- Deisolated by permitter.
- Returned to service.
These steps would have to be repeated across each asset on the list to be sampled.
Following review of the market, a “one size fits all” solution was not available. Therefore, in the case of this project, a solution was designed and implemented that allowed for the three criteria, outlined above, to be met—regardless of asset status, i.e., running or standby. Three separate pieces of hardware were required to achieve this:
- Sample probe: A sample probe was selected that allows for an uncontaminated sample to be taken from the correct location in the asset. Additionally, the use of the sample probe ensures repeatable data acquisition, and it can be adapted to ensure a sample is taken from the mixing zone. Different sample probe models and sizes were selected to match each asset to be sampled.
- Dry break fitting: A valved dry break fitting and cap was also mounted to each asset. This fitting allows for oil to be topped up after sampling or at any time, in conjunction with a cap to prevent contamination. A dedicated dry break fitting was matched to each oil grade and then rolled out to the relevant assets.
- Desiccant breather: Oil temperature within the reservoir will fluctuate, dependent on status. As a result, the pressure within the reservoir constantly changes, which can make oil sampling more challenging. The inclusion of a desiccant breather equalizes the pressure while also eliminating the potential for contamination that may result from each pressure change.
Integrating all three pieces of hardware together on an asset ensures that all three criteria outlined above are met, greatly speeds up the sampling process (thus reducing cost), and eliminates any impact to asset availability/access.
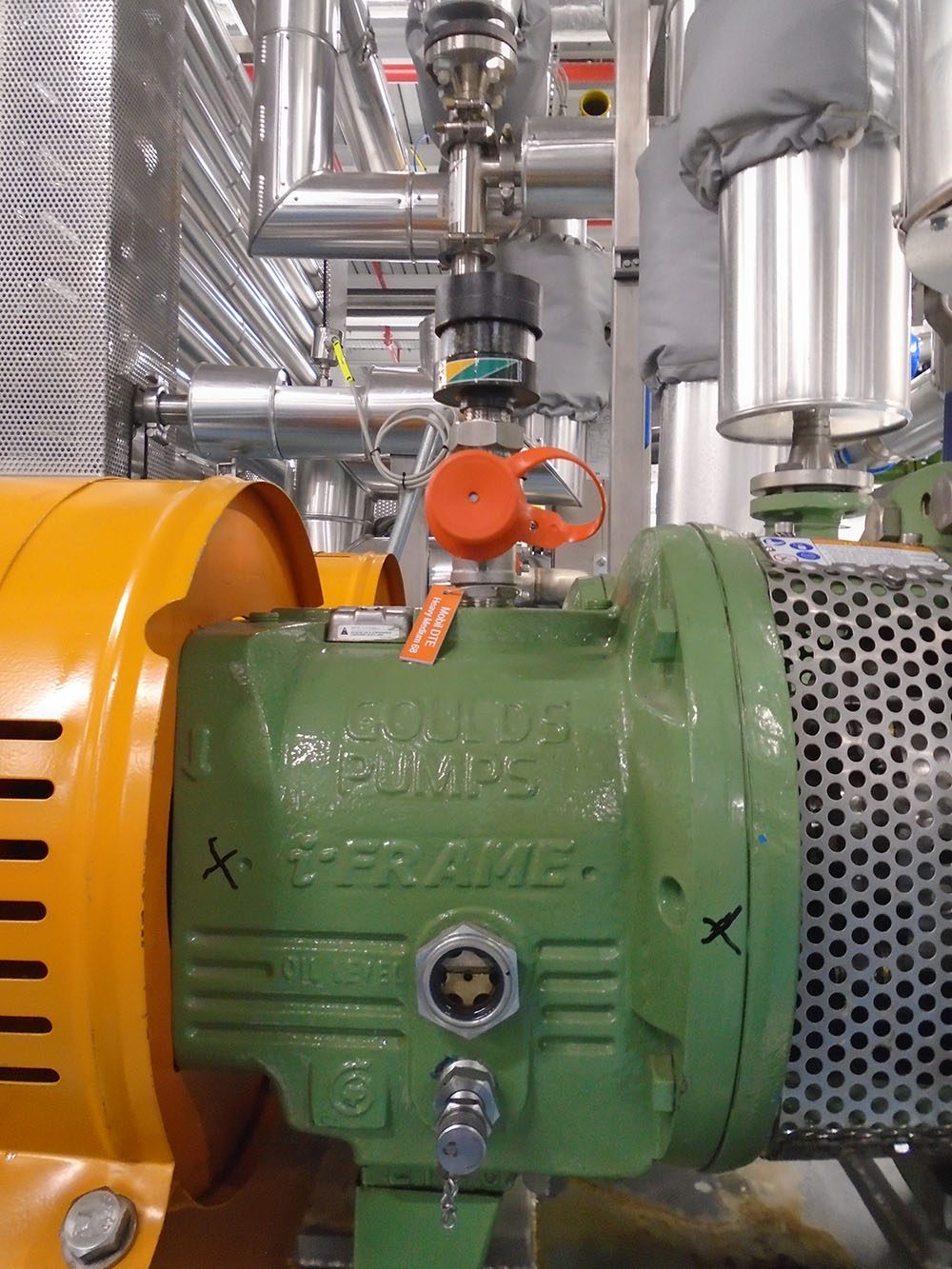
Figure 2: IE43 LGF Utility Waste Pump—Sample Point, Dry Break + Cap & Desiccant Breather
Wider applications
Excellence in lubrication management is the very foundation of rotating asset reliability. As such, monitoring the condition of a lubricating oil reveals key indicators of asset health that help guide decisions around its care and maintenance. However, these decisions are only as good as the data upon which they are based.
In the case of oil analysis, taking a safe, repeatable, and representative oil sample is more challenging than it may at first appear. It is not uncommon for a sample to degrade by 2-3 ranges due to poor sampling practices.
As such, the solutions outlined here can be applied anywhere that oil samples are obtained, e.g., Pharma & Life Sciences, MFG, Marine, Energy, Transport, Mining, Utilities. The same three criteria for data acquisition must be met across all industries and the assets therein for the benefit to be realized.
DATA is King
Good data is now and has always been the basis of key decisions in the maintenance/reliability world. Over the years, how that data is gathered has evolved—it has been automated, computerized, and is now online—but the SME’s ability to predict unscheduled downtime is only as good as the data available.
Furthermore, in a large, complex facility like Eli Lilly & Company’s IE43, trying to isolate where to focus effort is a constant challenge. The knowledge gained from the data gathered out of this CBM program has allowed the identification of issues associated with cross contamination, moisture ingress, particle contamination, premature wear, and other failure modes. But in addition, it has allowed the elimination of wasteful oil changes and identified areas for further improvement. Monitoring of the data generated and interpretation of trends from sample to sample by MLA II and MLA III certified personnel, allows for focused and timely interventions. Also, it provides a layer of confidence in decision making when used in conjunction with other CBM methodologies such as vibration monitoring.
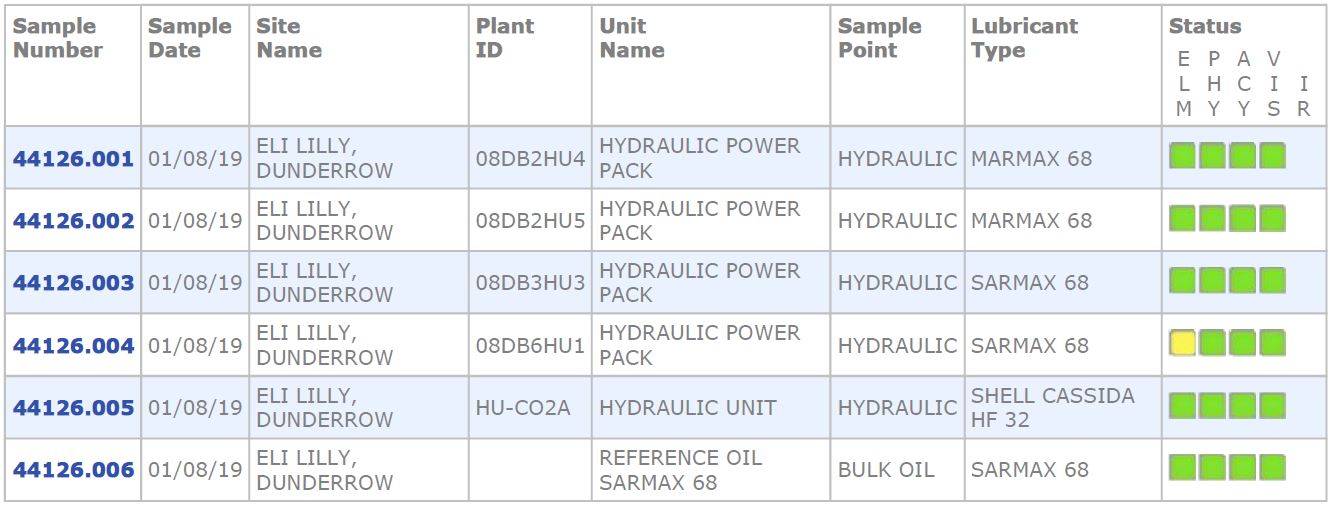
Figure 3: Oil Data Summary Sheet
Evolving Maintenance Strategy
The delivery of this project made it feasible to introduce a widespread oil sampling program in the IE43 facility. Oil sampling had, of course, been used in the past; however, it was always on an ad hoc, asset-by-asset basis. Widespread deployment had been too cumbersome as a result of all the steps to be completed for each asset to obtain one sample. This project has reduced those steps from seven to three:
- Sample requested by the maintenance team.
- Sample taken by craft.
- Oil top-up.
The asset doesn’t need to be returned to service as it never left service. Many are sampled while running.
In addition, the requirement of oil changes as part of routine PM activities has been eliminated. PM’s where oil changes were completed on a calendar basis have now been updated to ensure oil changes are only scheduled when the data indicates this is required. In this way the oil becomes part of the asset and not simply a consumable to be replaced.
Implementation
Safe and compliant roll-out of the hardware associated with this project was a key objective, but safe use of the assets into the future was also a consideration. Post implementation, only one permit is now required to execute a sample program, whereas previously up to 90 would have to be completed. Sampling and top-up are now much safer with spills being eliminated.
This project and the data generated from it has directly led to two CSI’s (Cost Saving Initiatives) onsite to date.
-
- The first CSI directly relates to the cost of program implementation, seeing a reduction of 45% (i.e., cost to gather samples from the list of assets) achieved within year one. The costs associated with the program in year two and subsequent years will be reduced by 47%. Note: Year one target is to get all assets to a stable status, sampling once a quarter. For year two and beyond the target is to maintain that stable condition while reducing PM frequency to six monthly.
- The second CSI relates to the elimination of oil changes on several assets. Oil changes will now occur based on oil sample data alone and not on fixed calendar dates as was the case in the past. A cost avoidance of €11,100 per annum was achieved here.
The implementation of the sampling PM has steadily improved also. At the last execution of this PM, data was gathered from 98% of assets on the list. The data gathered continues to show an improving trend, indicating that the facility is moving from a proactive to a truly condition-based status.
Finally, the requirement for oil changes has been eliminated, as detailed above. This has a positive environmental impact by significantly reducing hazardous waste generated, i.e., no more need to dispose of five hundred liters per year of used oil.
Embedding the Improvements
The completion of the Oil sampling PM in IE43 is now a standard part of maintenance execution, with a dedicated PM in place on CMMS. This PM has a dedicated Job Plan providing technical detail for craft on sample taking. Remediation where required will be documented through a linked follow-up Work Order, thus ensuring timely action and traceability.
More broadly, a lubrication management strategy is now embedded in the IE43 facility. The foundation of this is a site SOP controlling all aspects of lubrication management. This SOP has been built on the ICML 55.1 Standard. This management strategy sees lubricants managed from procurement through to the assets in the field with acceptance criteria identified. Furthermore, each lubricant is setup through a dedicated color code system from within the CMMS itself, through the oil handling equipment in the dedicated oil store to the asset—again, color-coded to match. This management system has been independently audited, being “considered world class” with a nine-fold increase in the overall score awarded, when compared to the baseline audit four years ago.
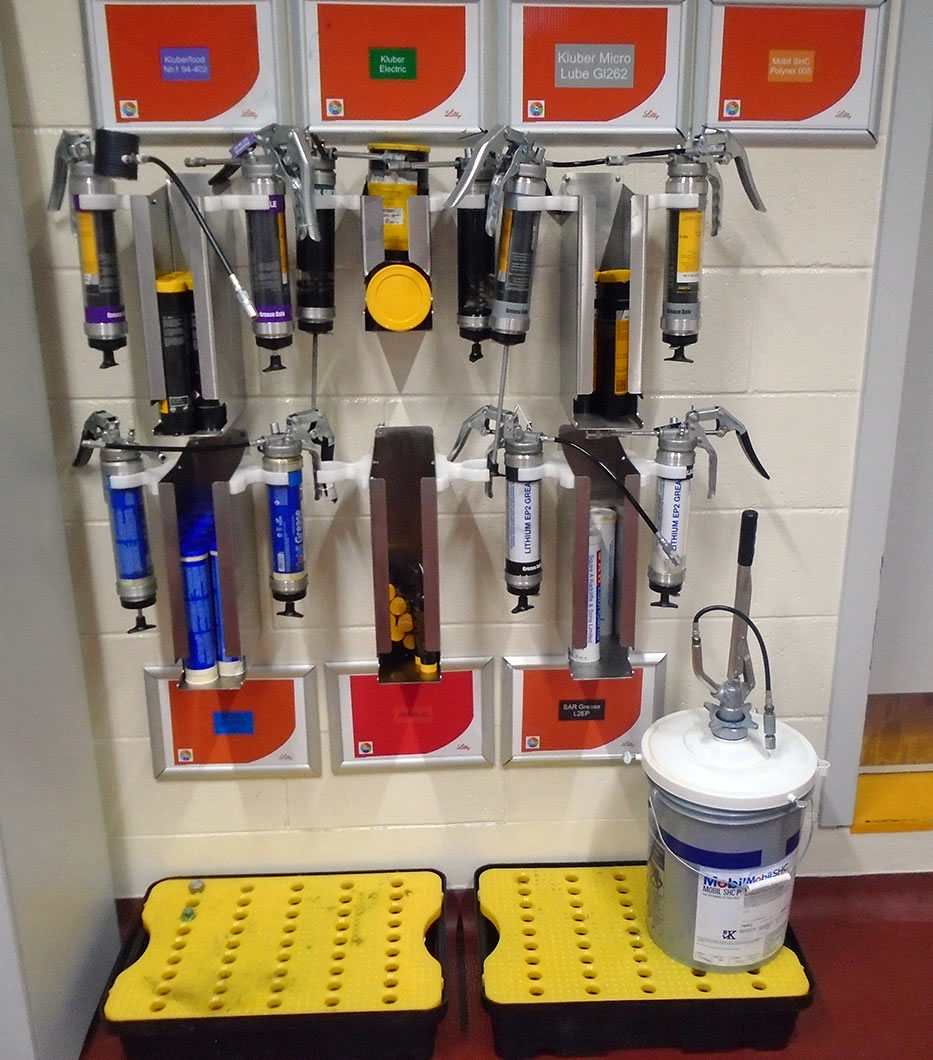
Figure 4: IE43 LGF Lube Room—Grease Storage
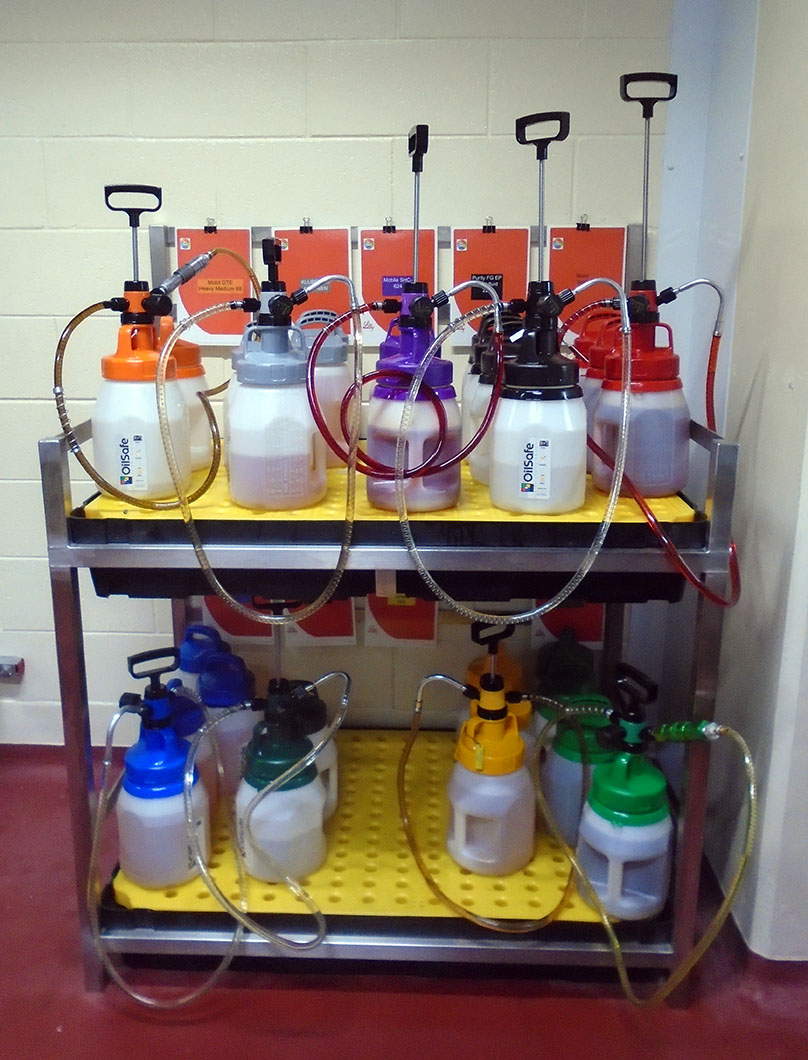
Figure 5: IE43 LGF Lube Room—Oil Storage
Finally, a technical appreciation of the challenges and skills required by all involved in the lubrication process within IE43 is ensured, as the site SOP is part of the online training program for all IE43 craft and engineers. Additional training courses have also been completed by all levels within the maintenance team by external experts to further enforce best practice.
Conclusions
Wide spread deployment of oil sampling routes can seem daunting at first. It is easy to find a list of reasons why it can’t work. However, a detailed understanding of your assets’ design and operation, coupled with a focus to find the right technical solutions, will yield results. Start by defining where you currently are (based on good data), be determined enough to drive necessary change, and success will be achieved.
Remember: lubrication management is a journey and not a destination!