Paul Hiller, ICML, March 22, 2022 | Perhaps it goes without saying that there is a correlation between the level of management support at a facility and the ease of implementing any sustainable lubrication program at that same facility.
A lubrication team’s success can be achieved more readily and quickly with a champion in the management team.
We often read case studies about such champions spearheading the audit and improvement of pre-existing lubrication programs. But when Blue Buffalo’s Heartland Pet Food Manufacturing received the 2020 John R. Battle Award for Lubrication Excellence, the occasion recognized a program that had been designed proactively from scratch, before the first machine was ever put into production.
Management priorities
The Heartland plant sits along Interstate 70, just northwest of Richmond, IN, USA. Site construction commenced with groundbreaking in mid-2016, and the facility made its first production run in December 2018. Thanks to a champion in management, the lubrication program developed from theory to reality during that year-and-a-half time span. While all-new machinery was still being acquired and installed, he was able to steer management to:
- prioritize proactive planning
- fund relevant hiring, training, and certifications
- establish synergistic partnerships with service providers
- implement a vision of wholistic solutions
“The plant manager came to this facility already having knowledge of what a world class lubrication [program] should be and what the benefits of that program would be,” says Kevin Keith, Lubrication Specialist at Heartland. “He promoted the idea of a lubrication program before the first machine was turned on.”
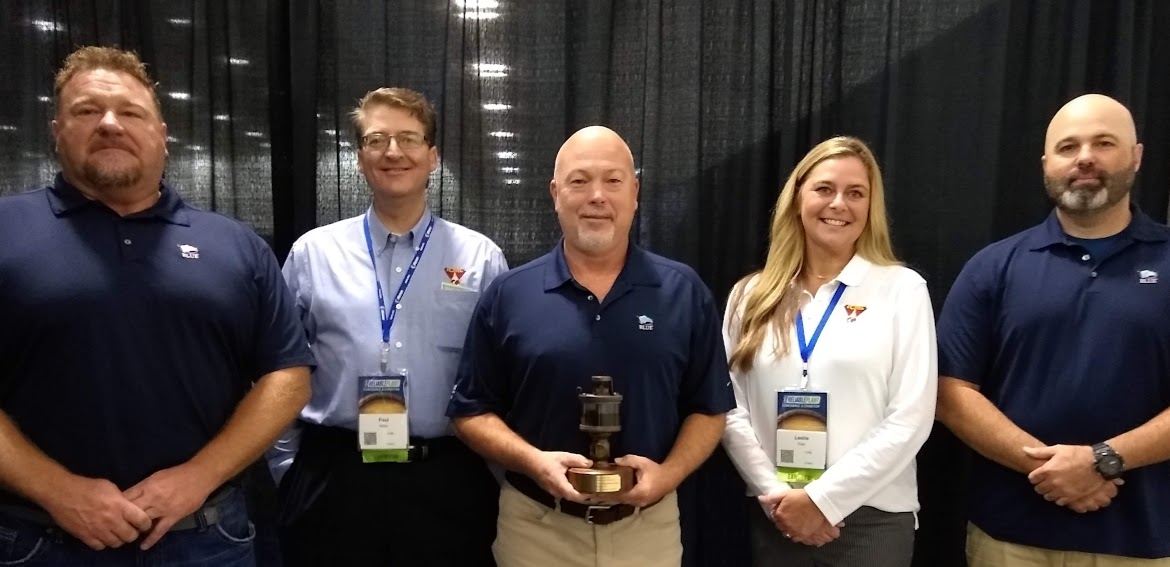
Figure 1: Blue Buffalo – Heartland was awarded ICML’s 2020 John R. Battle Award for Lubrication Excellence in October 2021. Shown here L-to-R are Conditioning Monitoring Technician Ray Jackson, ICML Marketing Manager Paul Hiller, Lubrication Specialist Kevin Keith (holding the Battle Award), ICML Executive Director Leslie Fish, and Reliability Specialist Bobby Beatty.
Keith was speaking of Travis Moore, who had received lubrication training prior to his arrival at Heartland, and who was instrumental as the driving force to develop a lubrication program for proactively. With a passion for lubrication excellence and an eye toward ensuring profitability by avoiding common shortcuts and missteps, Moore provided the necessary focus and management resources for his team to achieve optimum performance.
It starts with a culture of education
Under Moore’s direction, a culture of excellence was established up front and continues to this day. As Keith says, “The maintenance culture at Blue Buffalo is unlike any that I have ever been involved with. Most maintenance departments are entirely reactive, but our culture here is one of looking for ways to improve reliability through improvement of conditions and constant monitoring. This culture of cooperation is supported and driven by management and our company mission statement. This culture is one of the foundations of our company.”
“The first day of my new job was spent on an airplane, going to receive training in Portland, Oregon.”
Finding the right people to fit this culture is certainly key to the lube program’s success and sustainability, and that’s how Keith and his fellow lubrication specialist, Matthew Felix, came to be here. With the plant manager’s input, the company hired Felix in 2018 when the lubrication program was still in development, and Keith joined him the following year. While both men are currently certified by ICML—Keith holds MLA II and MLT II, while Felix holds MLA III and MLT II—that was not always the case.
“When I was hired as the second Lubrication Specialist, I had no experience or knowledge of what a lubrication program was,” recalls Keith. “The first day of my new job was spent on an airplane, going to receive training in Portland, Oregon. In my opinion, sending me to that training on my very first day in the lube program speaks volumes to the level of dedication toward an excellent lube program. Since that first training I have received many more [certifications] and look forward to obtaining my MLE at some point.”
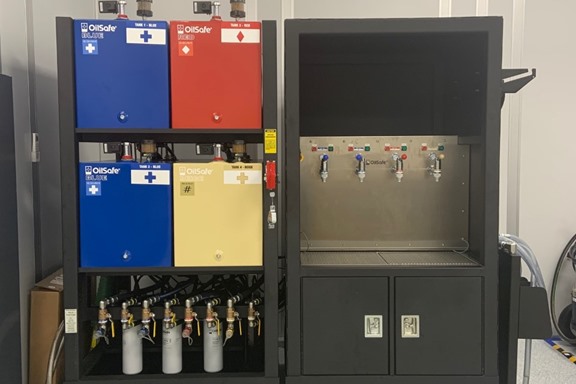
Figure 2: Oil Safe bulk oil storage system for Heartland’s most commonly used oils.
Keith notes that any training requested by the technicians has always been approved. “Education and training are key factors in the success of our lubrication program and are encouraged and supported by all levels of management,” he says. This is true not just for lubrication specialists but also for everyone with whom they interact, including operations, maintenance, and supervisors. Ultrasonic and laser alignment training has been conducted in-house by equipment manufacturer reps, while the oil analysis and machinery lubrication classes that Keith and Felix attended were provided by Noria Corporation off-site.
Blue Buffalo even offers a tuition reimbursement program that encourages employees to partake of job-related, continuous learning opportunities. According to Keith, “Continuing education is an important part of our system here and will continue to be encouraged and promoted. Learning is a lifelong journey and there are always new ideas and techniques to be gathered.”
“And this has been a very good investment,” he continues. “Although our plant is still young, we have had only a few machine failures so far and none has been attributed to lubrication issues.”
Practical partnerships with experienced providers
With little more than a year available during site construction, another supportive management decision to accelerate timely development of the impending lubrication program was to seek outside consultation suitable for Heartland’s circumstances. Not only would Heartland’s program have to address environmental food-grade concerns uncommon to other industries, but this was also an entirely new operation. Without an historic mix of old and new machinery, and without having to stem the tide of any longstanding, poor lubrication practices, the team was free to select its ideal operational partners based on merit and convenience.
“We set out to have a world class lubrication program from the start,” says Keith, “and, being a new facility, we had the luxury of starting with a good system.”
The team was free to select its ideal operational partners based on merit and convenience.
They selected Tulsa-based Noria Corporation not just for the aforementioned training courses, but also to guide them through all the decision-making necessary for a bespoke plan. “Noria helped us with the setup of our lubrication maintenance program, providing the roadmap to the highest level of improvements and standards that we [had established],” says Keith. With Noria’s recommended metrics, the lube team modified and retrofitted their new machines with breathers, fill ports, sight glasses, drain ports, etc., all before startup.
Admittedly, even best-laid plans require tweaks in real life, so the Heartland team has made some adjustments to the system in its first three years of operation. For instance, Keith says they subsequently added column sight glasses to replace the original 12mm sight glasses. But overall, with Noria’s initial guidance, Heartland’s management was able to “provide the necessary KPI’s and performance metrics to monitor performance” from the get-go, says Keith.
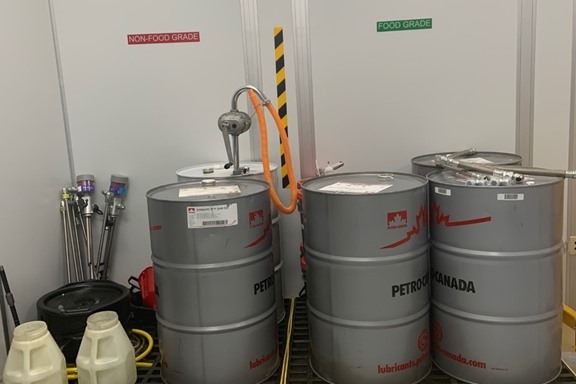
Figure 3: Oil drum storage for food safe and non-food safe oils.
Despite planning for roughly 1300 machinery units under their jurisdiction, the early lube team kept pre-selection of a lubricant supplier relatively simple. “Lubrication selection also began before the machines were started here at Blue,” says Keith. “We chose PetroCanada because of the additive package that would be beneficial to us because of the environment where the machines would be operating. Since we produce pet food here, our lubricants must also be food grade, and PetroCanada had the best selection of food-grade lubricants.”
“Additionally, PetroCanada is a local distributor,” he noted, “so they are very responsive to any need we may have, and they also take the waste oil.”
To stay on top of their food-grade environment, the lubrication plan would involve frequent oil sampling, so management approved a contract with POLARIS® Labs. “This choice was made because of the close proximity to our facility and the 48-hour turnaround on our samples,” Keith explains. “Alarms from Polaris Labs are cross referenced with our in-house cleanliness targets. Our oils are sampled monthly and filtered when the particle count warrants filtering. Contaminant levels are closely monitored as well, and if the levels are above our standards, the oil may be filtered or even subject to a complete drain and refill.”
Lubrication is only part of a wholistic strategy
Good management understands that lubrication is not a standalone function but is integrated within a broader condition monitoring context.
“Oil analysis, vibration analysis, thermography, and other condition monitoring specialists are a part of the same team at Blue, with a common leader or manager,” explains Keith. “This ‘reliability’ team functions together. The team may have technology specialization, but communication is clear between members. We recognize that it takes a whole set of tools to get the job done. We share data and try to maintain all data on a common database.”
“This culture of cooperation is supported and driven by management and our company mission statement. This culture is one of the foundations of our company.”
“We have two CBM technicians who monitor machine vibration and thermography through a remote system and through daily inspections of machines,” he continues. “Every machine in our facility is inspected at least weekly and more frequently depending on the criticality of the unit. Any problems that are detected by our conditions monitoring department or our lubrication specialists can be immediately addressed and corrected.”
So, as the lubrication specialists, what do Keith and Felix do all day?
According to Keith: “Our daily lube tasks are set up through Maintenance Connection CMMS software, with daily PMs assigned to both of us. The PM frequency was originally determined by Noria, but in a few cases, some adjustments were eventually made (primarily regarding the application of spray oil to roller chains). But, for the most part, the Noria PM system has worked very well for us.”
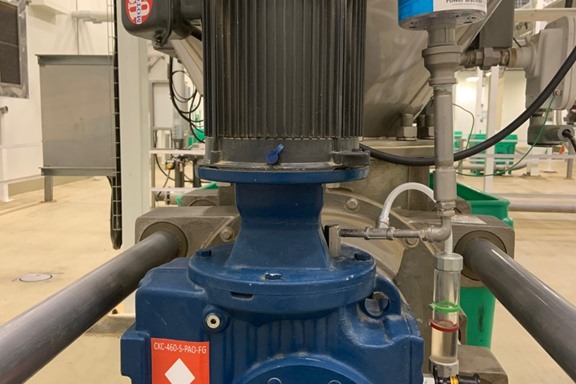
Figure 4: Fully modified gearbox with sample point, breather, column sight glass and return line, color coded oil ID sticker, fill and drain ports, and a sample point ID sticker.
Keith and Felix also depend on each other to mitigate human error. “Our facility is divided into two halves, Pre-Kill (raw, unprocessed ingredients) and Post-Kill (product that has been heated to kill all bacteria),” he says. “Each of us takes a side of the facility and performs the daily PMs that have been assigned to the areas on that side. Matt and I trade sides every day to have new eyes on the equipment so nothing is missed.”
These PMs may include sight glass and breather inspections, top-ups of gearboxes, greasing of roller bearings, thermal checks, and more. They also rotate the kidney-loop filtration carts as necessary. Larger projects that require downtime to perform, such as yearly drain and fills, are scheduled during the monthly cleaning day(s). These planned downtime events are one to two days long, so that is when machines are broken down and sanitized. This gives the maintenance department time to get into safety caged areas and lock-out machines that would normally be running.
Results have been positive, as Keith notes there have been “no hurdles” so far.
“We are lucky enough to have top-down support from management, and even if some managers or supervisors were not completely sold on the original idea, they have come on board because of the outstanding track record we have so far.”
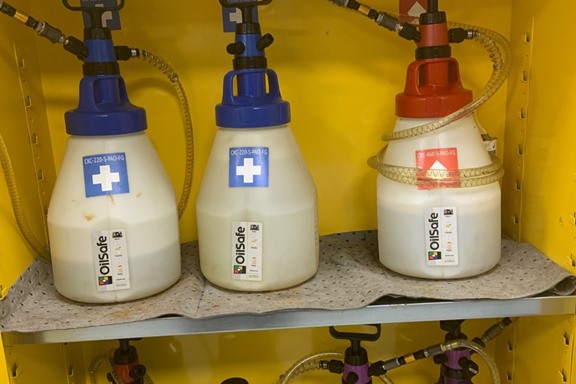
Figure 5: Fire safe cabinet storage of Oil Safe top up containers that are color coded and labeled for their specific oils.
Of course, being a new facility, Heartland has no historic track record that can be used to present a before-and-after comparison. “All our cost savings are based on what other companies have incurred without quality lubrication programs,” says Keith. “Infancy failure has been the biggest cause of failures here, and we have only had a few of those. The lack of downtime is the product of a good system and employees that take pride in their work and get along well with each other.”
Sustainable vision
Although Heartland’s original management champion, Travis Moore, has since left the company, Keith says he was inspired by Moore’s unwavering support, and he now exhibits his own healthy optimism for the future.
“Our plant manager told me he had a vision of making Blue Buffalo ‘world class in lubrication processes,’” he recalls. “I shared his vision in the beginning, but now I have expanded on his and have my own vision of making Blue Buffalo a world standard in the lubrication industry.”
“The path forward for Blue is to continue with as much education and learning as possible,” Keith promises. “We plan to stay up on the latest advancements in our industry by maintaining a broad outlook with as many sources of information on food safety, lubrication advancements, and personal safety that we can find. We will continue to fine tune our machinery and processes to the best of our ability. We will never be perfect with no room for improvement, but that to me is the fun and challenging part of my job.”